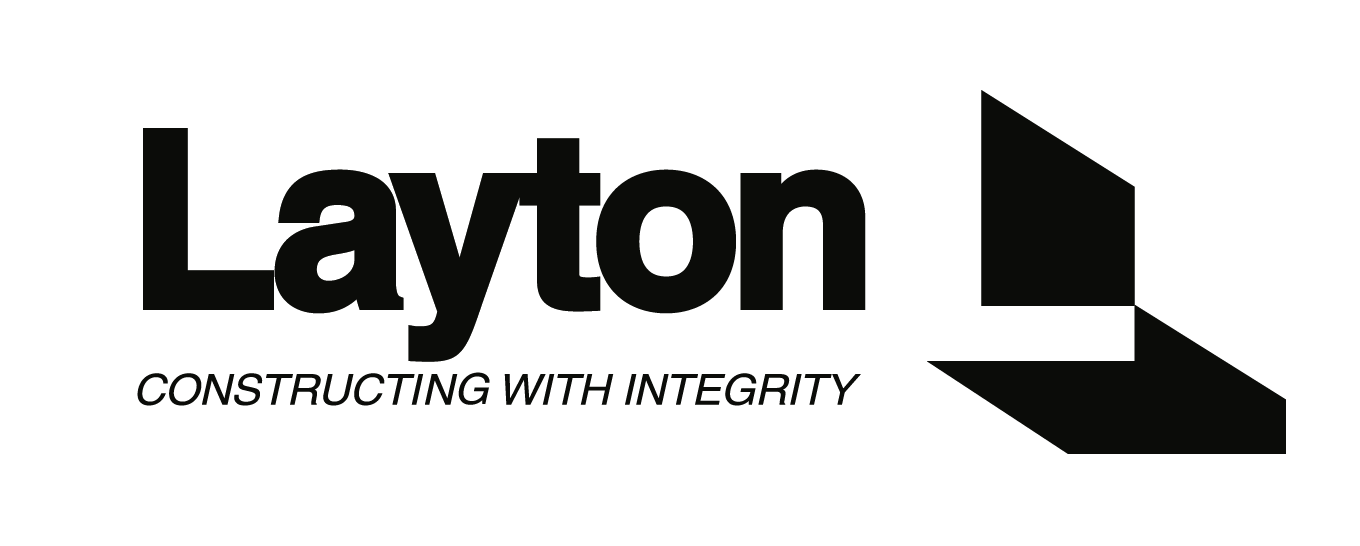
Layton Construction was tasked with a massive redevelopment at Phoenix’s Central Transit station. The 2.5-acre site, which is spread over 2.5 acres – will be home to a 32-story mixed-use tower and a 21-story student housing tower.
On this build site, the crew didn’t have a lot of space. So, timing deliveries was a finely choreographed exercise – when one was leaving, another was always waiting to get in. If there were any delays or disruptions to the schedule, it would throw the entire day off. This meant excess costs and workers standing around waiting for a delivery. That was something that they simply couldn’t afford.
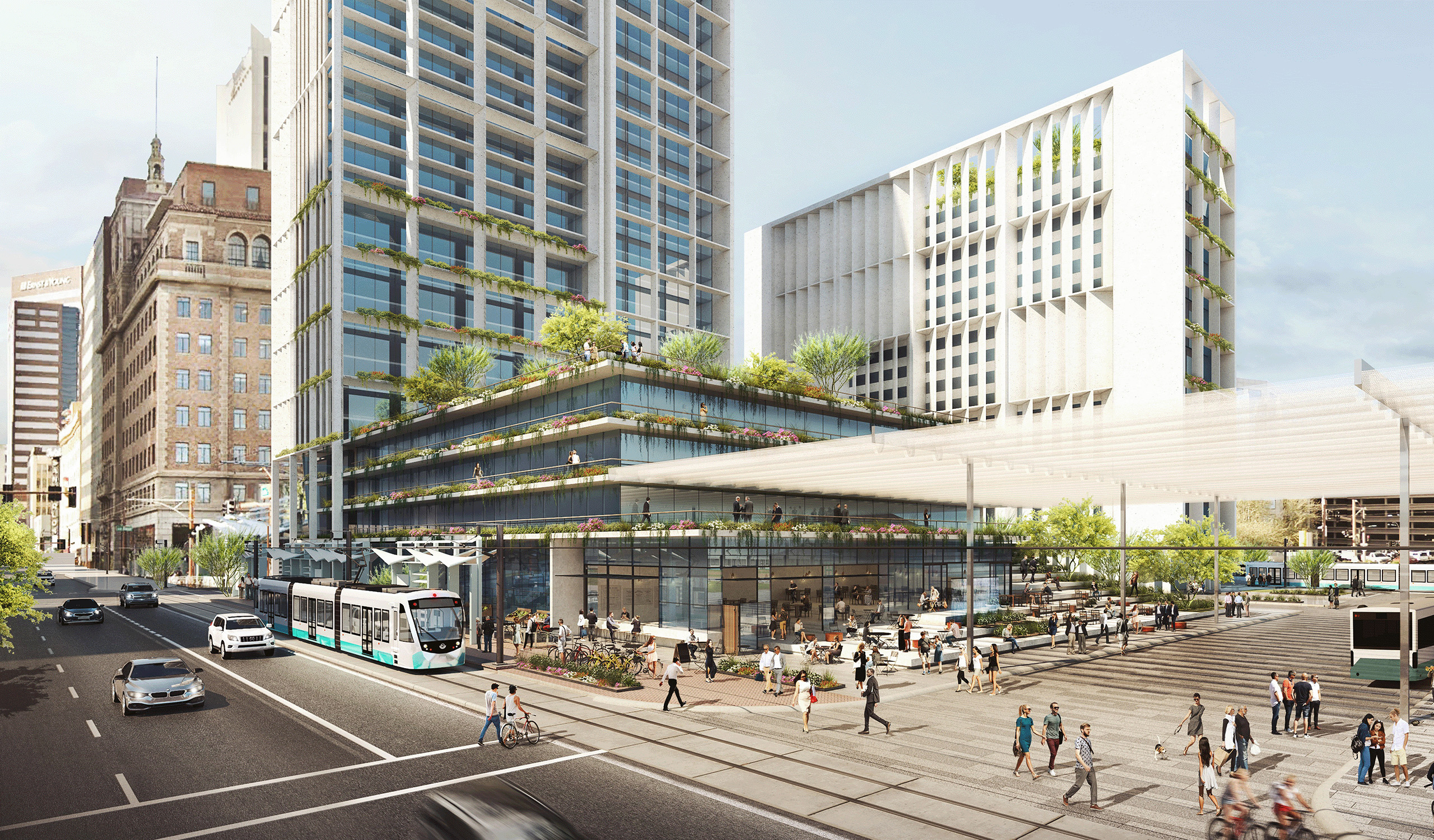
When everyone’s onboard, things are smoother
According to Jake Bayer, Site Logistics Manager for Layton Construction, the best thing about Veyor is being able to get all their key stakeholders and personnel on board. By coordinating everybody’s activities – not only in the field, but in the office, as well as distributors and manufacturers – it’s made life a whole lot easier. After the deployment of the software, workers are no longer waiting around for a delivery, meaning they could continue work, which saved the company valuable overheads. Similarly, deliveries weren’t backed up in the alleys or in the street waiting.
“Logistics wise, it's been 100% saving us time." - Jake Bayer, Site Logistics Manager
.png)
Delivering a fuss-free solution
Layton Constructions’ biggest problem was managing deliveries in such a tight part of the city which also had a live tram line running adjacent to the site – something that Veyor’s platform was able to solve. Veyor’s construction-site logistics software allows you to track drivers in real-time, get live updates on the ETA of deliveries and communicate the best route to your worksite, meaning you’ll know exactly when they’ll arrive. This will help you decide if you should let your team get on with another job or have them at the ready.
Bringing down crane costs
As with most construction sites, the crane was one of Layton’s biggest expenses. Making sure it was working efficiently was vital in order for successful completion of the project. Veyor’s crane scheduling features allow contractors, crane operators and site coordinators to see real-time planning and bookings. So, everyone can know when their pick is, when their next delivery is arriving and where it needs to go to. Saving everyone time, money and a whole heap of hassle.
“Once you have your delivery on-site, your tradesmen can continue working, instead of standing around waiting.” - Jake Bayer, Site Logistics Manager
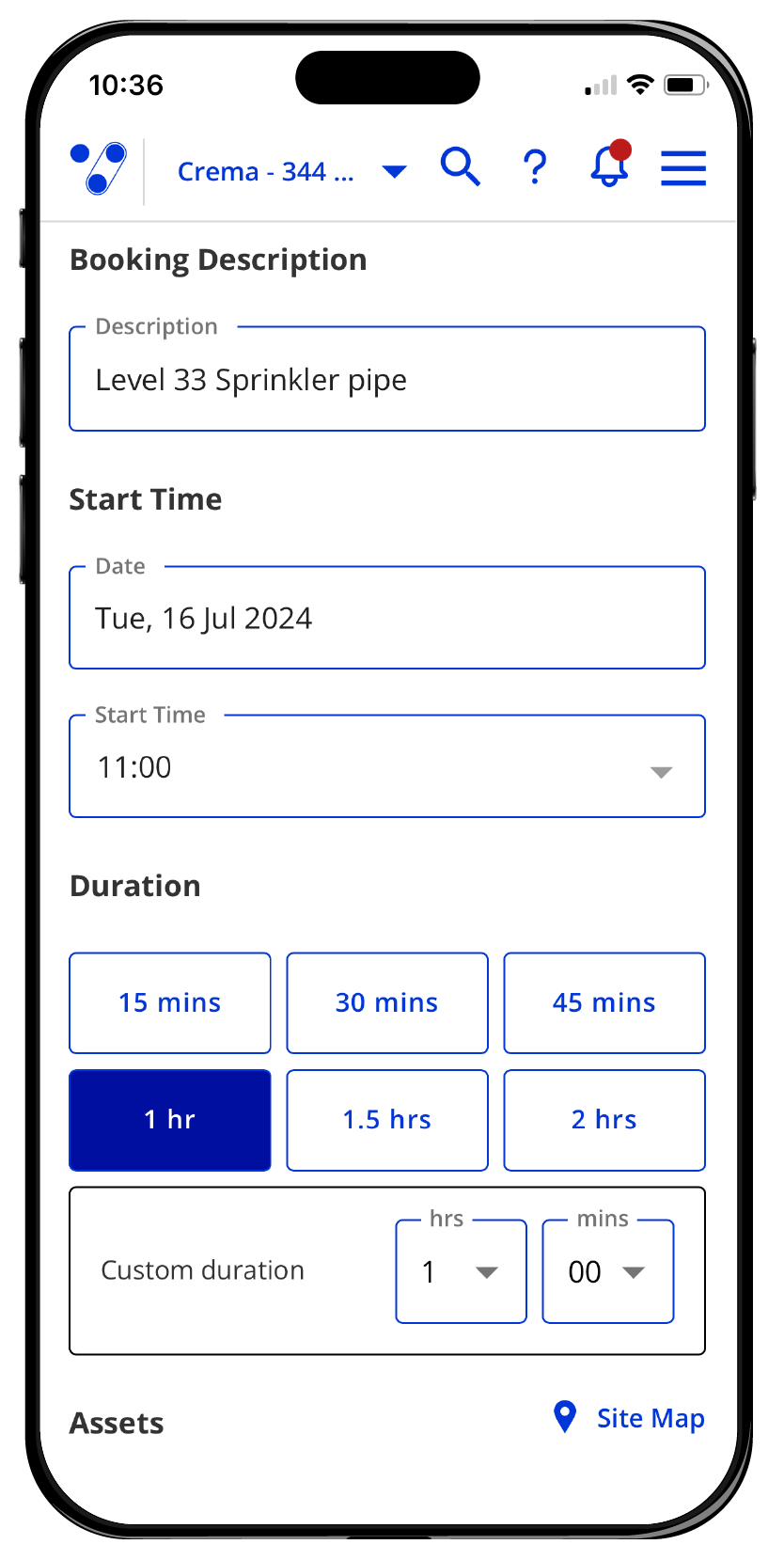
Bringing subcontractors into the 21st century
It isn’t just Layton Construction that rates Veyor highly: their subcontractors also think it’s fantastic, and after a few weeks, they were using the systems like seasoned pros. This is a whole lot better than the yesteryear, when they were relying on inefficient communication methods like whiteboards, emails or phone calls to try and coordinate their logistics. As Layton Construction discovered, Veyor’s construction logistics software helps you avoid delays, clashes and cancellations - to keep your project on track.
“After two or three weeks, everyone was onboard and everybody liked it." - Jake Bayer, Site Logistics Manager
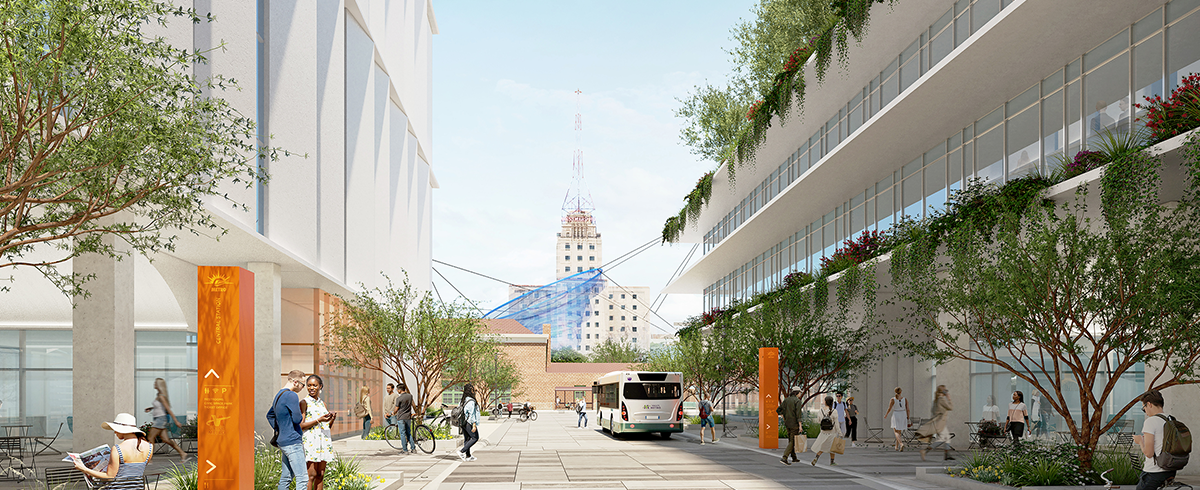