As we’re sure you’ve already heard, modular construction is on the rise. This means stick-built construction is now making way for modular building systems that are utilising modern, prefabrication techniques.
Modular construction usually takes place in a factory environment and as a result of this, current construction supply chains which have traditionally focused on the delivery of raw materials to sites are now making way for new, more time-critical logistics systems.
How Does Off-Site Construction Work?
Just like traditional construction, off-site construction can’t happen without careful planning, designing, fabricating, transporting and assembling building elements for rapid site assembly.
When it comes to building off-site, modular construction is the most widely used, with up to 95% in some cases, shipped and assembled as 3D volumetric units that are later joined on-site. The modular industry consists of two distinct industry segments: Relocatable Modular and Permanent Modular.
Relocatable Modular is used for temporary space needs (think job site trailers, temporary classrooms, communication pods and showrooms) and Permanent Modular is more widely used across high rises, government buildings, health-care facilities, schools, hotels etc.
Let’s Talk Off-Site Logistics
Off-site construction is a building process of delivery as much as it is an amalgamation of building products.
As more building is done off-site, the importance of construction logistics continues to grow. For example, the construction program critically relies on each component of the building to be transported and fixed in a strict sequential order. Therefore, effective, streamlined logistics is critical, so that delivery of prefabricated modular components can be pre-planned and then tracked and monitored in line with the program. With a platform like Veyor, we can make this happen across the entire supply-chain in real time.
So What are the Benefits?
There’s some big benefits to off-site construction but there’s some notable disadvantages too.
If we’re focusing on the thumbs up’s there’s some incredible pro’s as below:
- Shorter construction schedules
- Greater degree of predictability in cost
- Reduced material waste
- Reduced carbon emissions due to transportation to and from site associated with on-site construction
- Reduced site disturbance
- An increase of safety and security of labourers and trade equipment
And if we’re looking at the thumbs’s down here’s what to also note below:
- Structural bulkiness: floor to floor heights and wall thicknesses affected
- Transportation restrictions limit module and panel size
- Spans and configurations of design can be restricted
- Lack of transparency in overhead, profit margin, transport, setting (cranes), and associated increase in designer fees if new to the process
- Flexibility and changeability of structure through future renovations becomes more difficult
All in all when understood and developed by stakeholders intentionally, and with early project planning, off-site construction looks to be a promising new solution to potentially keep project schedules and budgets in check - whilst also increasing quality and reducing environmental impact.
It’s looking to be particularly effective when used on repetitious or unique projects, with teams that are prepared to embrace the challenges and opportunities associated with it’s delivery.
Reach out to Veyor today to find out more about how we can help you make work happen when it comes to off-site logistics in modular construction.
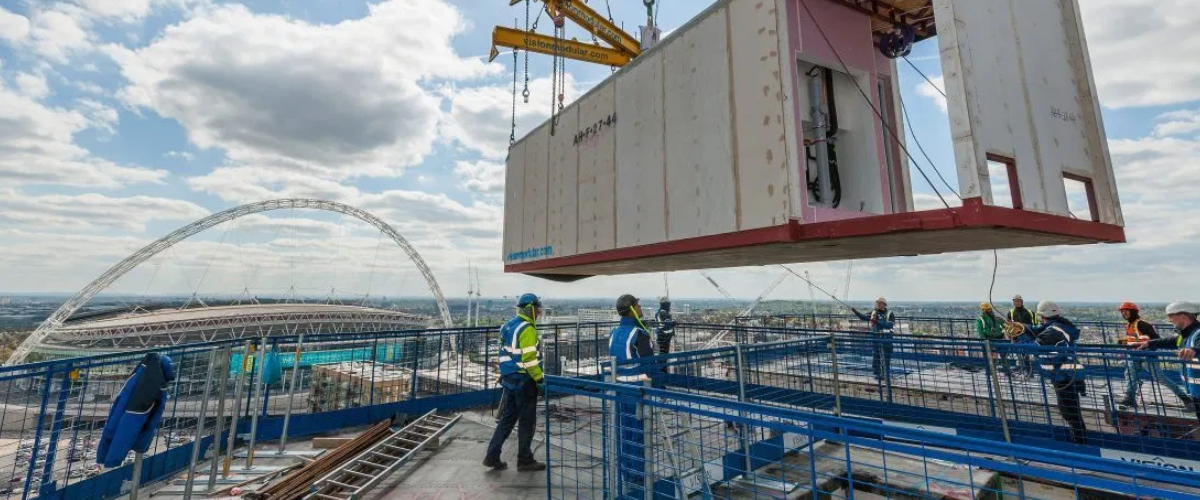